OEM Transfers – How Does It Work?
- Who is GDCA, and why has my customer requested a product transfer?
- We EOL’d the product because there were no parts available; what makes you think you can build it?
- How are we going to structure the transfer?
- How do we determine technical data licensing or transferring fees?
- In a typical transfer of technical data, do you require on-site training?
- Once the transaction is complete, OEM will not need to be re-engaged anymore, right?
- If we agreed to transfer technical data, would we still be able to build and ship the product if we wanted to? What does that arrangement look like?
Who is GDCA, and why has my customer requested a product transfer?
GDCA is a legacy equipment manufacturer (LEM) with more than 30 years of experience extending the life of discontinued embedded products for customers who have demand for designs that span well beyond the Original equipment manufacturer (OEM) support.
Customers come to us when their product has been discontinued but who still require a guarantee of extended product availability and support, sometimes for 15–20 years beyond EOL.
OEMs work with us to fulfill extended support contracts and/or support ad-hoc customer requirements for designs whose low-volume demand and increasing supply chain instability make no business sense to support. GDCA is a LEM and protects the OEM’s relationship with their customer while ensuring that the demands of supporting and delivering orders of discontinued products do not reroute resources already assigned to support core products.
We EOL’d the product because there were no parts available; what makes you think you can build it?
The first step in the process is to provide the customer a Sustainment Options Report in which we analyze the demands of the client, the product availability, and the feasibility of restarting the manufacturing line.
We will need to develop an understanding of the technical and financial challenges of manufacturing (i.e., test fixture, availability of components, and customer requirements) to determine if sustaining the board is feasible. To do this, we need access to the product’s BOM and test procedure from you, the OEM. This is typically done under an NDA.
How are we going to structure the transfer?
We have been doing transfers for 30 years and have become extremely efficient at transferring the technical data with limited OEM support. The first step is to locate the technical data, the BOM, test procedure documentation, and confirmation of what test hardware is available for transfer. Once we have this information, we can come to an agreement on the licensing fees.
How do we determine technical data licensing or transferring fees?
We use the BOM, test procedure documentation/equipment inventory, and sales history to determine the value of the technical data. The licensing terms can be either an up-front fee, royalties, or a mix of both, depending on what the OEM wants.
In a typical transfer of technical data, do you require on-site training?
Normally, yes, we will require one day for engineering access and on-site training if the test equipment is available for transfer. This might not require a full day; it all depends on the complexity of the design and testing process. However, during these pandemic times, we have been doing this work remotely over the course of a few days.
Once the transaction is complete, OEM will not need to be re-engaged anymore, right?
Correct. GDCA is responsible for any customer support needs going forward.
If we agreed to transfer the technical data, would we still be able to build and ship the product if we wanted to? What does that arrangement look like?
Normally, once the technical data is transferred, it is because the OEM does not want to build the product anymore because it is not cost-effective. Therefore, the license is typically exclusive for GDCA to manufacture. However, we are flexible with the agreement to make sure the OEM and customer are supported appropriately.
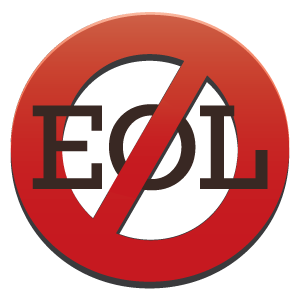
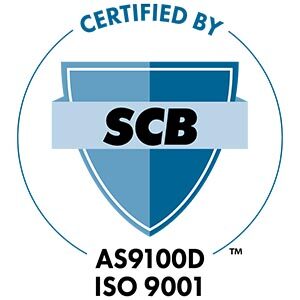
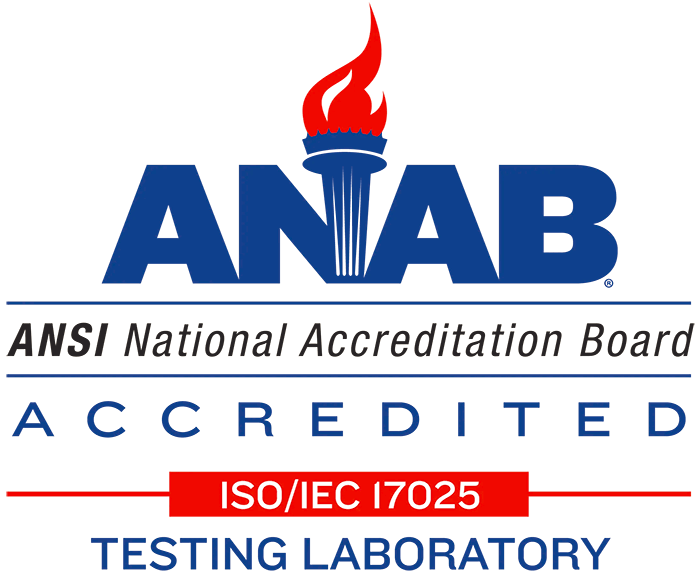
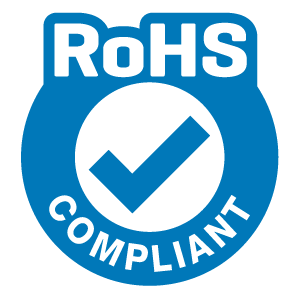
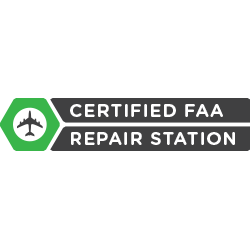
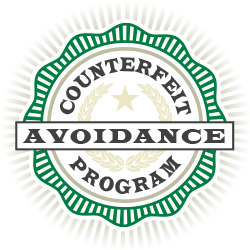
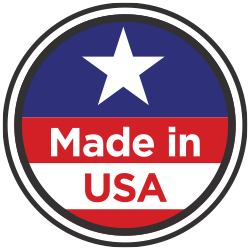